Mon, 10 Mar 2025 15:30:22 +0100
When heat exchanger plates accumulate deposits such as scale, sludge, or biological growth, thermal resistance increases, reducing heat transfer efficiency. This leads to higher energy consumption, requiring more power to maintain process temperatures.
2. Prevention of Equipment Damage
Fouling can cause uneven heating, excessive pressure drops, and localized overheating, leading to material degradation and potential failure of plates and gaskets.
3. Process Integrity and Product Quality
Industries such as pharmaceuticals and food processing require stringent cleanliness standards. Contaminated heat exchangers can compromise product quality and safety.
4. Reduction in Maintenance and Downtime
Regular cleaning minimizes unexpected failures, reducing downtime and costly repairs. Planned maintenance ensures continuous operation without disruptions.
See our cleaning machines for plate and frame
Understanding the types of fouling helps determine the best cleaning approach.
1. Scaling
Hard mineral deposits, primarily calcium and magnesium carbonates, accumulate on plate surfaces, creating insulating layers that hinder heat transfer.
2. Biological Fouling (Biofouling)
Bacteria, algae, and other microorganisms can form biofilms on the plates, reducing heat exchanger efficiency and increasing the risk of corrosion.
3. Particulate Fouling
Suspended solids, dirt, and debris in the fluid can settle on the plates, restricting flow and reducing performance.
4. Chemical and Corrosion Fouling
Corrosive substances in the process fluid can react with the metal plates, leading to material degradation and deposit formation.
5. Oil and Grease Contamination
In applications involving lubricants or oil-based fluids, grease buildup can obstruct fluid pathways, diminishing efficiency.
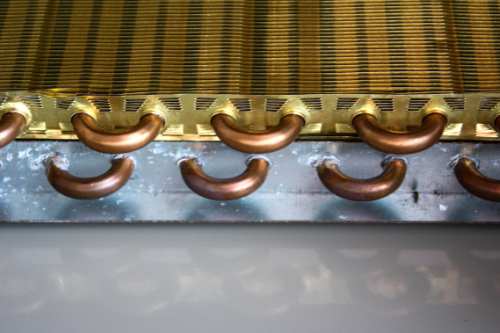
1. Manual Cleaning (Disassembly and Mechanical Cleaning)
This method involves dismantling the heat exchanger, removing individual plates, and manually cleaning them with brushes, high-pressure water jets, or specialized cleaning tools.
Steps:
Effective for heavily fouled units.
Allows inspection for damage and wear.
Cons:
Time-consuming and labor-intensive.
Requires skilled personnel to prevent gasket and plate damage.
2. Chemical Cleaning (CIP – Clean-In-Place)
Chemical cleaning involves circulating a specialized cleaning solution through the heat exchanger without dismantling it. This method is highly effective for removing scale, biofouling, and oil contamination.
Steps:
Non-invasive; does not require disassembly.
Faster cleaning process compared to manual cleaning.
Cons:
Requires proper chemical selection to avoid material damage.
Ineffective for severe fouling requiring mechanical removal.
3. Ultrasonic Cleaning
Ultrasonic cleaning is an advanced method that uses high-frequency sound waves to generate cavitation bubbles in a cleaning solution. These bubbles implode on the plate surfaces, effectively dislodging contaminants without causing damage.
Steps:
Pros:
Highly effective for removing stubborn deposits.
Gentle on delicate plate surfaces.
Reduces the need for aggressive chemicals.
Cons:
Requires specialized ultrasonic equipment.
Not suitable for cleaning in place; plates must be removed.
4. High-Pressure Water Jet Cleaning
This method uses pressurized water to remove accumulated deposits from the heat exchanger plates.
Steps:
Environmentally friendly, as it minimizes chemical use.
Effective for removing loose debris and soft deposits.
Cons:
May not remove hardened scale or stubborn grease effectively.
Risk of plate damage if pressure is too high.
Need help with your plate and frame heat exchanger cleaning?
Regular Inspection and Monitoring
- Periodically check pressure drops across the heat exchanger, as increasing pressure losses indicate fouling.
- Inspect gaskets and plates for wear, cracks, or leaks.
Routine Cleaning Schedule
- Establish a preventive maintenance plan based on operating conditions.
- Use CIP cleaning at scheduled intervals to prevent severe fouling.
Use High-Quality Fluids
- Ensure process fluids are filtered to reduce particulate contamination.
- Treat water sources to minimize scale formation.
Optimize Operating Conditions
- Maintain appropriate flow rates to reduce sedimentation.
- Avoid temperature extremes that promote fouling or corrosion.
Invest in Advanced Cleaning Technologies
- Ultrasonic cleaning and CIP systems enhance cleaning efficiency while minimizing downtime.
Work with Professional Service Providers
- Engaging specialized cleaning service providers ensures thorough maintenance and extends equipment lifespan.
Plate and frame heat exchangers play a critical role in industrial processes, but their efficiency can be severely impacted by fouling. Regular cleaning using the right method—whether manual, chemical, ultrasonic, or high-pressure washing—is essential for maintaining performance and preventing costly downtime. Implementing a proactive maintenance strategy, optimizing fluid conditions, and utilizing advanced cleaning technologies can significantly enhance the longevity and efficiency of heat exchangers.
By adopting best practices and leveraging innovative cleaning solutions, industries can minimize operational disruptions, reduce maintenance costs, and ensure sustainable, high-performance heat exchanger operation. Investing in proper cleaning and maintenance ultimately translates into better efficiency, reduced energy consumption, and extended equipment lifespan. DCM Ultrasonic, plate and frame heat exchanger cleaning experts.
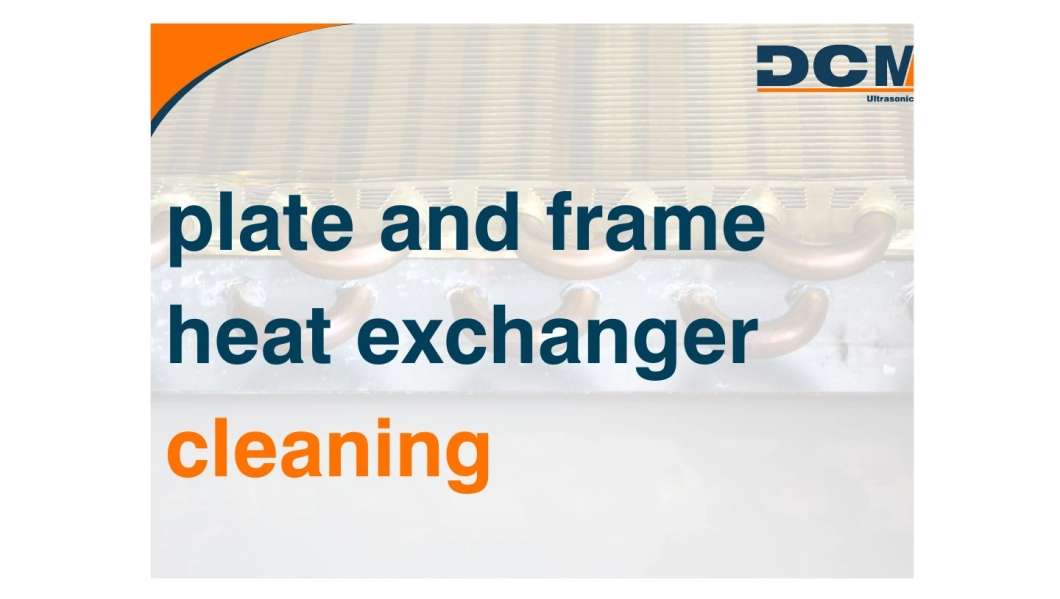
News
plate and frame heat exchanger cleaning
10 March de 2025
Plate and frame heat exchangers (PFHEs) are widely used across various industries, including power generation, food processing, pharmaceuticals, and HVAC systems. These devices facilitate efficient heat transfer between two fluids without direct contact. However, over time, fouling and contamination can significantly reduce their performance, leading to energy losses, increased maintenance costs, and potential system failures. Regular cleaning is crucial to maintaining efficiency, prolonging equipment lifespan, and ensuring optimal operation.Why plate and frame heat exchanger cleaning is Essential
1. Efficiency and Energy SavingsWhen heat exchanger plates accumulate deposits such as scale, sludge, or biological growth, thermal resistance increases, reducing heat transfer efficiency. This leads to higher energy consumption, requiring more power to maintain process temperatures.
2. Prevention of Equipment Damage
Fouling can cause uneven heating, excessive pressure drops, and localized overheating, leading to material degradation and potential failure of plates and gaskets.
3. Process Integrity and Product Quality
Industries such as pharmaceuticals and food processing require stringent cleanliness standards. Contaminated heat exchangers can compromise product quality and safety.
4. Reduction in Maintenance and Downtime
Regular cleaning minimizes unexpected failures, reducing downtime and costly repairs. Planned maintenance ensures continuous operation without disruptions.
See our cleaning machines for plate and frame
Common Types of Fouling in Plate and Frame Heat Exchangers
Understanding the types of fouling helps determine the best cleaning approach.1. Scaling
Hard mineral deposits, primarily calcium and magnesium carbonates, accumulate on plate surfaces, creating insulating layers that hinder heat transfer.
2. Biological Fouling (Biofouling)
Bacteria, algae, and other microorganisms can form biofilms on the plates, reducing heat exchanger efficiency and increasing the risk of corrosion.
3. Particulate Fouling
Suspended solids, dirt, and debris in the fluid can settle on the plates, restricting flow and reducing performance.
4. Chemical and Corrosion Fouling
Corrosive substances in the process fluid can react with the metal plates, leading to material degradation and deposit formation.
5. Oil and Grease Contamination
In applications involving lubricants or oil-based fluids, grease buildup can obstruct fluid pathways, diminishing efficiency.
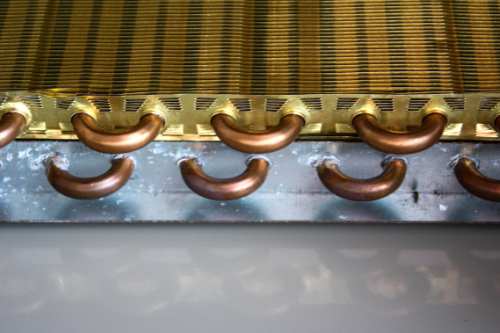
Cleaning Methods for plate and frame heat exchanger cleaning
1. Manual Cleaning (Disassembly and Mechanical Cleaning)
This method involves dismantling the heat exchanger, removing individual plates, and manually cleaning them with brushes, high-pressure water jets, or specialized cleaning tools.
Steps:
- Turn off the system and isolate the heat exchanger.
- Carefully disassemble the unit and remove plates.
- Inspect each plate for deposits, damage, and gasket wear.
- Use mechanical scrubbing or pressure washing to remove fouling.
- Rinse and dry before reassembling the unit.
Effective for heavily fouled units.
Allows inspection for damage and wear.
Cons:
Time-consuming and labor-intensive.
Requires skilled personnel to prevent gasket and plate damage.
2. Chemical Cleaning (CIP – Clean-In-Place)
Chemical cleaning involves circulating a specialized cleaning solution through the heat exchanger without dismantling it. This method is highly effective for removing scale, biofouling, and oil contamination.
Steps:
- Identify the appropriate chemical solution (acidic for scale, alkaline for grease, biocide for biological growth).
- Connect a cleaning circulation system to the heat exchanger.
- Pump the cleaning solution through the unit for a set duration.
- Flush with clean water to remove residual chemicals.
Non-invasive; does not require disassembly.
Faster cleaning process compared to manual cleaning.
Cons:
Requires proper chemical selection to avoid material damage.
Ineffective for severe fouling requiring mechanical removal.
3. Ultrasonic Cleaning
Ultrasonic cleaning is an advanced method that uses high-frequency sound waves to generate cavitation bubbles in a cleaning solution. These bubbles implode on the plate surfaces, effectively dislodging contaminants without causing damage.
Steps:
- Submerge heat exchanger plates in an ultrasonic cleaning tank filled with a specialized cleaning solution.
- Activate the ultrasonic waves, which create microscopic bubbles that remove fouling from plate surfaces.
- Rinse the plates with clean water and dry before reinstallation.
Pros:
Highly effective for removing stubborn deposits.
Gentle on delicate plate surfaces.
Reduces the need for aggressive chemicals.
Cons:
Requires specialized ultrasonic equipment.
Not suitable for cleaning in place; plates must be removed.
4. High-Pressure Water Jet Cleaning
This method uses pressurized water to remove accumulated deposits from the heat exchanger plates.
Steps:
- Disassemble the heat exchanger and remove the plates.
- Use a high-pressure water jet to clean each plate surface thoroughly.
- Inspect for remaining contaminants and repeat if necessary.
Environmentally friendly, as it minimizes chemical use.
Effective for removing loose debris and soft deposits.
Cons:
May not remove hardened scale or stubborn grease effectively.
Risk of plate damage if pressure is too high.
Need help with your plate and frame heat exchanger cleaning?
Best Practices - plate and frame heat exchanger cleaning
Regular Inspection and Monitoring- Periodically check pressure drops across the heat exchanger, as increasing pressure losses indicate fouling.
- Inspect gaskets and plates for wear, cracks, or leaks.
Routine Cleaning Schedule
- Establish a preventive maintenance plan based on operating conditions.
- Use CIP cleaning at scheduled intervals to prevent severe fouling.
Use High-Quality Fluids
- Ensure process fluids are filtered to reduce particulate contamination.
- Treat water sources to minimize scale formation.
Optimize Operating Conditions
- Maintain appropriate flow rates to reduce sedimentation.
- Avoid temperature extremes that promote fouling or corrosion.
Invest in Advanced Cleaning Technologies
- Ultrasonic cleaning and CIP systems enhance cleaning efficiency while minimizing downtime.
Work with Professional Service Providers
- Engaging specialized cleaning service providers ensures thorough maintenance and extends equipment lifespan.
Plate and frame heat exchangers play a critical role in industrial processes, but their efficiency can be severely impacted by fouling. Regular cleaning using the right method—whether manual, chemical, ultrasonic, or high-pressure washing—is essential for maintaining performance and preventing costly downtime. Implementing a proactive maintenance strategy, optimizing fluid conditions, and utilizing advanced cleaning technologies can significantly enhance the longevity and efficiency of heat exchangers.
By adopting best practices and leveraging innovative cleaning solutions, industries can minimize operational disruptions, reduce maintenance costs, and ensure sustainable, high-performance heat exchanger operation. Investing in proper cleaning and maintenance ultimately translates into better efficiency, reduced energy consumption, and extended equipment lifespan. DCM Ultrasonic, plate and frame heat exchanger cleaning experts.