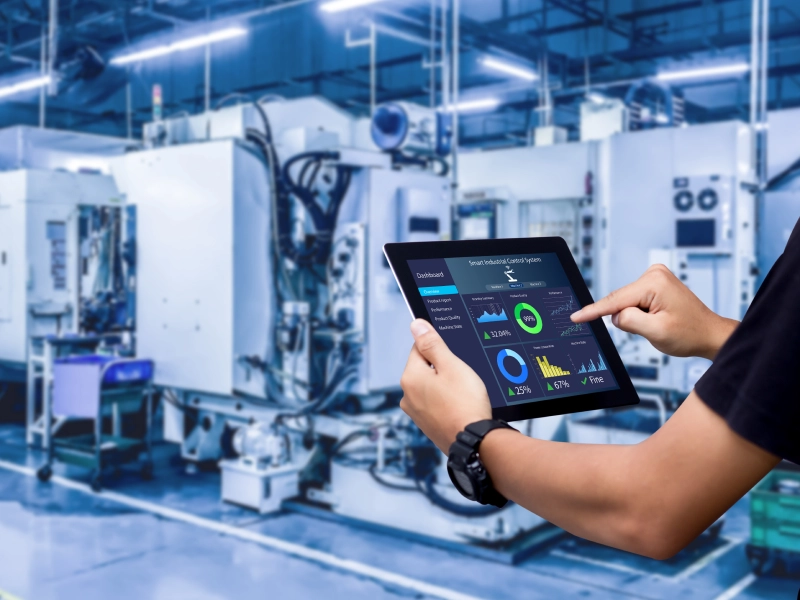
Other Services
Support and maintenance
Support and maintenance are critical aspects of any service or product, especially in the case of customized equipment and systems. Here are some key elements involved in support and maintenance:
1. Customer Service: Provide a dedicated point of contact for customers to report problems, ask questions and request technical support. This service may be available via phone, email, online chat, or a ticket system.
2. Updates and improvements: Keep your computer up to date with the latest software or hardware improvements and updates. This may involve implementing security patches, new features, or performance improvements.
3. Inspections and preventive maintenance: Perform regular equipment inspections to identify and address any potential problems before they become serious problems. This may include cleaning, lubricating, adjusting components, and performing functional tests.
4. Repairs and technical service: Provide fast and efficient repair services in the event of equipment failure or breakdown. This may include component repair or replacement, problem diagnosis, and calibration services.
5. User Training: Provide training and resources so users can use the equipment effectively and safely. This may include user manuals, instructional videos, in-person or online training sessions, and reference materials.
6. Service contracts: Offer customized service contracts that include a combination of the services mentioned above. These contracts can be tailored to the specific needs of each client, providing an appropriate level of support and maintenance to ensure optimal operation of the equipment over time.
1. Customer Service: Provide a dedicated point of contact for customers to report problems, ask questions and request technical support. This service may be available via phone, email, online chat, or a ticket system.
2. Updates and improvements: Keep your computer up to date with the latest software or hardware improvements and updates. This may involve implementing security patches, new features, or performance improvements.
3. Inspections and preventive maintenance: Perform regular equipment inspections to identify and address any potential problems before they become serious problems. This may include cleaning, lubricating, adjusting components, and performing functional tests.
4. Repairs and technical service: Provide fast and efficient repair services in the event of equipment failure or breakdown. This may include component repair or replacement, problem diagnosis, and calibration services.
5. User Training: Provide training and resources so users can use the equipment effectively and safely. This may include user manuals, instructional videos, in-person or online training sessions, and reference materials.
6. Service contracts: Offer customized service contracts that include a combination of the services mentioned above. These contracts can be tailored to the specific needs of each client, providing an appropriate level of support and maintenance to ensure optimal operation of the equipment over time.
Common errors when using an ultrasonic cleaning machine
When purchasing and using an ultrasonic cleaning machine, you must take into account various factors and avoid oversights that may affect the operation of your industrial ultrasonic machine. These are the 5 most common errors made by users when using ultrasonic cleaning machines:
- Using inappropriate detergents: many users purchase an ultrasonic cleaning machine and do not know which detergent to use for the part or surface they want to clean.
- Overloading the tank: exceeding the maximum load limit that your machine can support.
- Not degassing the liquid: cleaning liquid interferes with cavitation and reduces the efficiency of the process.
- Using an incorrect liquid level: transducers can be damaged and cavitation will be poor.
- Not performing periodic maintenance: not cleaning the tank regularly or not checking the condition of the transducers can lead to major problems in the operation of the cleaning machine. If you currently have a cleaning machine from another company, DCM Ultrasonic can help you maintain it correctly. Just contact us and we will help you solve your problem.
Effective support and maintenance not only ensures continued operation of equipment, but can also help extend its life, minimize downtime, and maximize return on investment for the customer.
CHECK OUT OUR LATEST MAINTENANCE PERFORMED IN BARCELONA
Support and maintenance of ultrasonic equipment
At DCM Ultrasonic, we know that the efficiency and durability of an ultrasonic cleaning machine depends largely on proper maintenance and specialized technical support. Therefore, we offer a comprehensive technical assistance service to ensure the optimal operation of our equipment and maximize its useful life.Our Technical Support available for you - Support and maintenance of ultrasonic equipment
- Remote assistance: Diagnosis and problem solving via telephone or video call.
- On-site support: Our specialized technicians travel to the client's facilities.
- Personalized training: Training for staff in the use and maintenance of the machine.
- Supply of original spare parts: We guarantee the availability of high-quality components.
- Scheduled maintenance contracts: Annual plan options to prevent failures and improve performance.
We solve any type of problem you have with machines from other brands
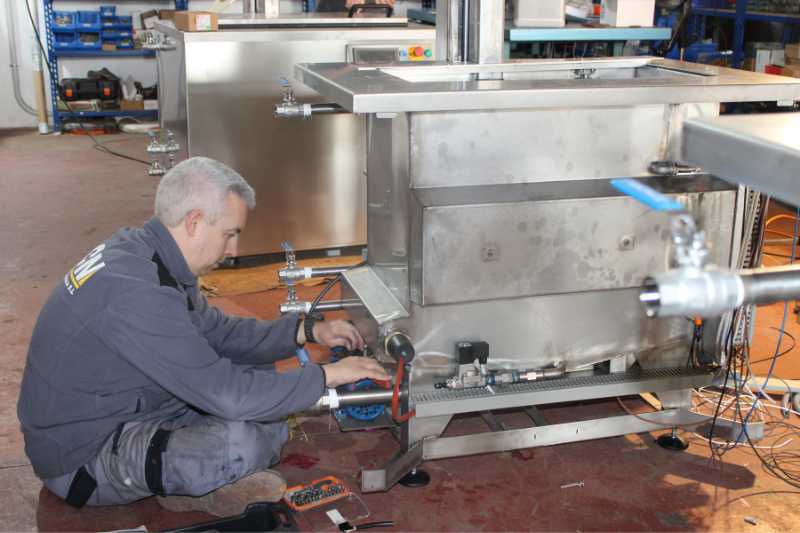
Tips for the proper use of your ultrasonic equipment for industrial cleaning
1. Use the Right Cleaning Liquid
The cleaning liquid is a crucial factor for the success of the ultrasonic process. Using specific detergents for each type of dirt and material improves the results without damaging the parts or the machine's tank. Avoid the use of corrosive or inappropriate products that can reduce the efficiency of the ultrasonic system.
2. Maintain the Optimal Bath Temperature
Each type of dirt requires an adequate temperature to be effectively removed. In general, temperatures between 40°C and 60°C help improve cavitation without affecting the integrity of sensitive components. Use the machine's temperature control function to achieve the best efficiency.
3. Avoid Overloading Parts
Loading too many parts into the ultrasonic tank can reduce the effectiveness of the cleaning, as it hinders the uniform propagation of the ultrasonic waves. Place the parts without touching each other, allowing the cavitation to act evenly over the entire surface.
4. Perform Periodic Maintenance
To ensure consistent performance, it is vital to perform regular maintenance. This includes:
- Changing the cleaning fluid when necessary.
- Cleaning the filters and removing accumulated residue in the tank.
- Checking the status of the generator and ultrasonic emitters to detect possible failures.
5. Take Advantage of Scheduled Cleaning Cycles
Many DCM Ultrasonic machines have programmable cleaning modes that optimize energy consumption and process efficiency. Set the appropriate times and frequencies according to the type of dirt and material, avoiding unnecessary cycles that can wear out the machine.