Catalogue
Ultrasonic defoaming system - Foam control
Increases productivity and efficiency on packaging lines for bottles, juices, canning, and brewery. Ultrasonic technology with low energy cost and low operating cost for the food industry. Foam control for packaging and bottling lines.
Foaming on packaging lines for beverages such as beers, juices, and other carbonated beverages is a common challenge that affects production efficiency, accurate filling, and waste reduction. DCM Ultrasonic presents you with an effective solution to increase productivity in your factory.
DCM Ultrasonic's ultrasonic defoaming system employs high-frequency ultrasonic waves to destabilize the foam on the surface of the liquid during the packaging process. Through the controlled application of ultrasonic energy, the microbubbles collapse before they can form a stable foam layer, allowing for faster and more efficient filling. Foam control in processing plants and production lines.
This process occurs without physical contact with the product, which guarantees food safety, consistency in filling and reduction of product losses. In addition, the ultrasonic technology does not alter the organoleptic properties of the liquid, ensuring that the drink maintains its original taste, aroma and quality.
REQUEST MORE INFORMATION ABOUT OUR ULTRASONIC DEFOAMING SYSTEM
1. Real-time foam reduction
Minimizes the generation of foam in bottling, avoiding spills and product losses.
2. Optimization of the filling process
It speeds up bottling by allowing for more accurate and faster filling without interruptions due to foam build-up.
3. Increased efficiency and productivity
It reduces waiting times and allows you to maintain a constant flow on the production line.
4. Compatibility with various beverages
It works with beers, juices, soft drinks, fermented beverages, and other products that generate foam in the packaging.
5. Sustainability and waste reduction
It reduces product losses and improves the efficiency of raw material use, contributing to more sustainable production.
6. Reduced maintenance
Its design with no moving parts in contact with the liquid allows for minimal maintenance and longer system life.
7. Adaptability to different production lines
It is easily integrated into new or existing bottling lines without the need for major modifications.
Technical points for breweries
Foaming on packaging lines for beverages such as beers, juices, and other carbonated beverages is a common challenge that affects production efficiency, accurate filling, and waste reduction. DCM Ultrasonic presents you with an effective solution to increase productivity in your factory.
Ultrasonic defoaming system
The ultrasonic foam control system in the filling and packaging processes is designed to significantly reduce the foam in the bottles or cans during the packaging process, generating a more compact foam that is densely adhered to the can or bottle. This enables the system to deliver significant increases in productivity, reduced product waste, reduced pollution, and energy and water savings.DCM Ultrasonic's ultrasonic defoaming system employs high-frequency ultrasonic waves to destabilize the foam on the surface of the liquid during the packaging process. Through the controlled application of ultrasonic energy, the microbubbles collapse before they can form a stable foam layer, allowing for faster and more efficient filling. Foam control in processing plants and production lines.
This process occurs without physical contact with the product, which guarantees food safety, consistency in filling and reduction of product losses. In addition, the ultrasonic technology does not alter the organoleptic properties of the liquid, ensuring that the drink maintains its original taste, aroma and quality.
REQUEST MORE INFORMATION ABOUT OUR ULTRASONIC DEFOAMING SYSTEM
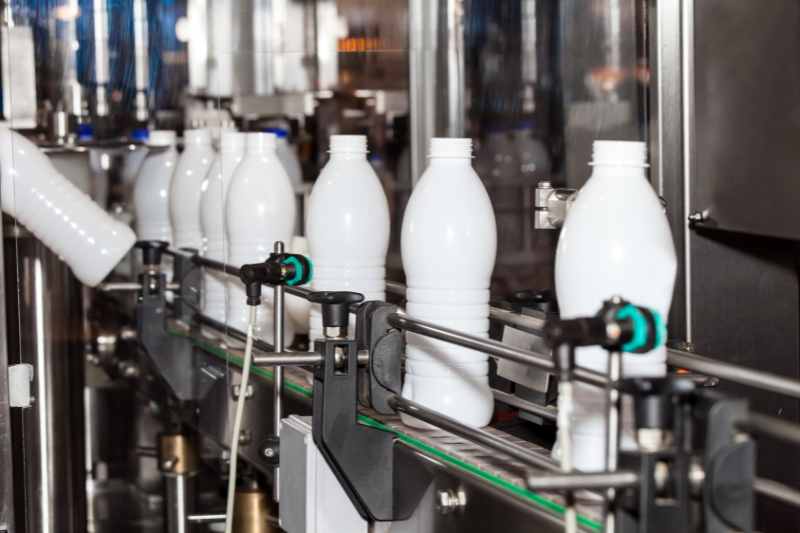
Benefits of DCM Ultrasonic Defoaming System
1. Real-time foam reductionMinimizes the generation of foam in bottling, avoiding spills and product losses.
2. Optimization of the filling process
It speeds up bottling by allowing for more accurate and faster filling without interruptions due to foam build-up.
3. Increased efficiency and productivity
It reduces waiting times and allows you to maintain a constant flow on the production line.
4. Compatibility with various beverages
It works with beers, juices, soft drinks, fermented beverages, and other products that generate foam in the packaging.
5. Sustainability and waste reduction
It reduces product losses and improves the efficiency of raw material use, contributing to more sustainable production.
6. Reduced maintenance
Its design with no moving parts in contact with the liquid allows for minimal maintenance and longer system life.
7. Adaptability to different production lines
It is easily integrated into new or existing bottling lines without the need for major modifications.
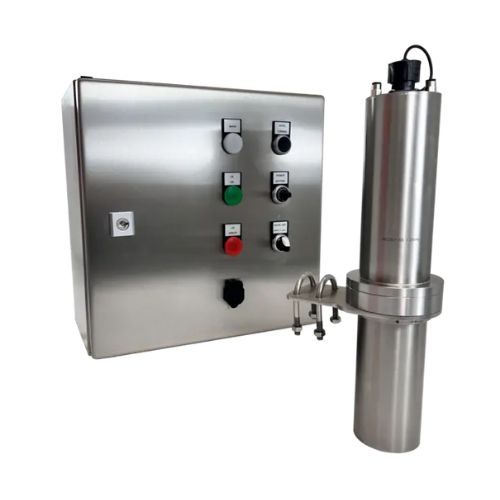
Applications of ultrasonic defoamer in food sectors
- Beer sector
Technical points for breweries
- Applicable to any type of filler: standard rotary fillers, aseptic or hot filling lines, linear fillers.
- No external cooling is required for the transducer system in the filling line
- The installation time of the foam control unit is fast, which means minimal line downtime.
- Applicable to glass, RGB, PET, cans, carton and bags packaging materials.
- Easy to install on existing bottles, cans, or other packaging lines
- Beverage sector
- Dairy Dryer
Features of the ultrasonic defoaming system
- High-power ultrasonic generators with frequency adjustment adaptable to different types of beverages.
- Ultrasonic emitters designed for industrial applications, optimized for high-speed bottling lines.
- Stainless steel construction to comply with hygiene and safety regulations in the food and beverage industry.
- Modular and scalable system, allowing it to adapt to different production speeds and packaging formats.
Machine series
Catalogue
Download our catalog with all the information about our technology, equipment and applications.
Can we help you with anything else?
Call without obligation at 960 26 36 65 or contact us through the form
COMPARISON TABLE
![]() UDM 30K NexTgenView Product |
![]() UDM 20K NexTgenView Product |
|
Ultrasonic Power (W) | 300 | 300 |
Frequency (KHz) | 30 | 20 |
Generator included | NexTgen | NexTgen |
Emitter External Dimensions (LxWxH) | 418x76x173 | 418x76x173 |
Generator External Dimensions (LxWxH) | 380x380x210 | 380x380x210 |
Emitter/Generator Total Weight (KG) | 6/15.4 | 6/15.4 |
Products
Equipment range
Where to use our industrial ultrasonic cleaning equipment
Work Areas - Ultrasonic cleaning
Contact
How can we help you?
Do you have any questions or queries about our industrial ultrasound equipment or our ultrasonic cleaning machines? Do you need to hire our services? Contact us using this simple form, we will reply as soon as possible. Thank you!!