Mon, 12 May 2025 15:34:49 +0200
Ultrasonic degreasing is a cleaning process based on ultrasonic cavitation, a technique that uses high-frequency sound waves (generally between 20 and 80 kHz) transmitted through a cleaning fluid. These waves generate millions of microscopic bubbles that implode near the surface of the submerged parts, effectively dislodging particles of grease, oil, wax, carbon, or other adhering residue, even in hard-to-reach areas.
This method offers extremely thorough cleaning without the need for harsh chemicals or mechanical pressure, making it an ideal option for delicate or complex components.
Degreasing is a fundamental step in many industrial processes. Metal parts and other components manufactured or used in industrial environments are often coated with cutting oils, lubricating greases, or solid residues after use or manufacturing. If these contaminants are not properly removed, they can compromise subsequent processes such as painting, welding, assembly, or the general operation of the equipment.
In sectors such as automotive, aviation, and precision component manufacturing, effective degreasing is crucial to ensure the quality of the final product and extend the life of the parts.
MACHINES FOR DEGREASING MECHANICAL AND INDUSTRIAL PARTS
Ultrasonic waves generate a phenomenon called cavitation, which involves the formation of millions of tiny air bubbles in the cleaning fluid. These bubbles compress and collapse violently, releasing a large amount of energy. This energy acts directly on the dirt, grease, or carbon adhering to the surface of the parts, effectively removing them without damaging the material. Once the parts are submerged in the tank, the ultrasonic waves create millions of microbubbles that implode on the surface of the parts. This phenomenon, known as cavitation, dislodges contaminant particles without the need for friction or direct contact.
This process produces a micro-brushing effect on the treated surfaces. Since the bubbles are less than 1 micron in size, they are able to reach even the smallest holes and corners. For this reason, ultrasonic cleaning is the most effective method for degreasing metal parts and components with complex geometries, regardless of the type of material: cast iron, steel, aluminum, copper, bronze, titanium, engineering plastics, or even rubber.
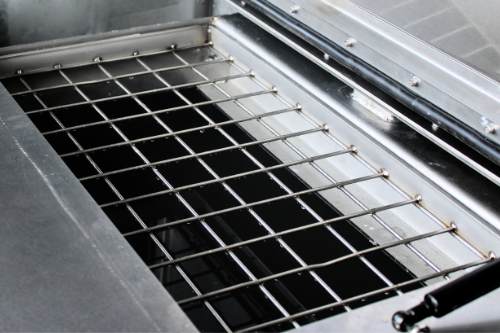
Ultrasonic tank for degreasing parts.
1. Deep Cleaning Even in Inaccessible Areas
Ultrasonic cavitation acts evenly across the entire surface of the part, including cavities, grooves, holes, threads, internal geometries, and rough surfaces. This ensures complete and even cleaning.
2. Respect for Parts: No Wear or Deformation
Without mechanical contact, parts are not scratched, deformed, or damaged, making it perfect for delicate or high-precision components, such as optical, electronic, medical, or watchmaking parts.
3. Energy Efficiency and Sustainability
Modern ultrasonic equipment like that of DCM Ultrasonic is designed to consume less energy than other industrial cleaning methods. Furthermore, the use of biodegradable detergents and liquid recirculation systems reduce the use of chemicals and the environmental impact.
4. Reduction in Cleaning Times
Ultrasonic degreasing is a fast process. Parts are cleaned in just a few minutes, significantly increasing plant productivity.
5. Automation and Labor Savings
Ultrasonic systems can be fully automated, eliminating the need for constant operator intervention. This allows human resources to be dedicated to more critical tasks and reduces occupational hazards.
6. Adaptability to Different Sectors
From heavy industry to the manufacturing of microelectronic components, ultrasonic degreasing is a versatile technology that adapts to very diverse needs and part sizes.
Ultrasonic degreasing has established itself as the best alternative to traditional industrial cleaning methods, thanks to its precision, effectiveness, speed, and respect for parts and the environment. For both maintenance tasks and manufacturing processes, this technology represents a smart and profitable investment for any industry.
Are you looking to improve the efficiency of your industrial cleaning processes? Do you want to remove tough contaminants without damaging your parts? Ultrasonic degreasing is the answer. Contact us and discover how our ultrasonic machines can transform your operations.
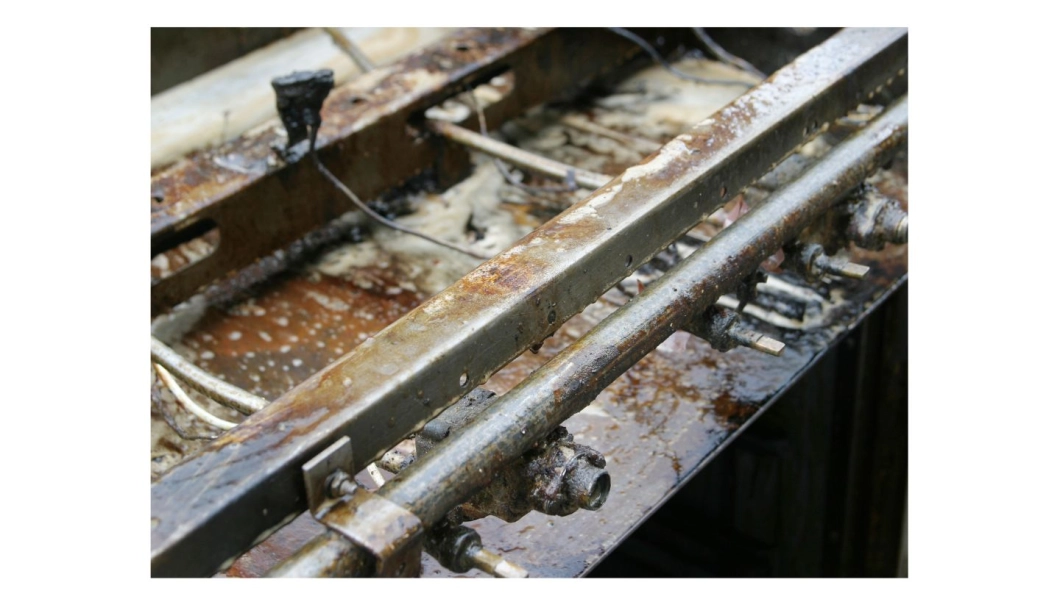
News
Ultrasonic Degreasing: Effective Technology for Industrial Cleaning
12 May de 2025
Ultrasonic degreasing has become one of the most effective, sustainable, and precise methods in industrial cleaning processes. Thanks to its ability to deeply remove oils, grease, and other contaminating residues without damaging parts, this technology has gained an essential place in multiple sectors, from automotive to aeronautics, including the medical and electronics industries.What is ultrasonic degreasing?
Ultrasonic degreasing is a cleaning process based on ultrasonic cavitation, a technique that uses high-frequency sound waves (generally between 20 and 80 kHz) transmitted through a cleaning fluid. These waves generate millions of microscopic bubbles that implode near the surface of the submerged parts, effectively dislodging particles of grease, oil, wax, carbon, or other adhering residue, even in hard-to-reach areas.
This method offers extremely thorough cleaning without the need for harsh chemicals or mechanical pressure, making it an ideal option for delicate or complex components.
Why is degreasing important in industry?
Degreasing is a fundamental step in many industrial processes. Metal parts and other components manufactured or used in industrial environments are often coated with cutting oils, lubricating greases, or solid residues after use or manufacturing. If these contaminants are not properly removed, they can compromise subsequent processes such as painting, welding, assembly, or the general operation of the equipment.
In sectors such as automotive, aviation, and precision component manufacturing, effective degreasing is crucial to ensure the quality of the final product and extend the life of the parts.
MACHINES FOR DEGREASING MECHANICAL AND INDUSTRIAL PARTS
How does an ultrasonic degreasing machine work?
Ultrasonic waves generate a phenomenon called cavitation, which involves the formation of millions of tiny air bubbles in the cleaning fluid. These bubbles compress and collapse violently, releasing a large amount of energy. This energy acts directly on the dirt, grease, or carbon adhering to the surface of the parts, effectively removing them without damaging the material. Once the parts are submerged in the tank, the ultrasonic waves create millions of microbubbles that implode on the surface of the parts. This phenomenon, known as cavitation, dislodges contaminant particles without the need for friction or direct contact.
This process produces a micro-brushing effect on the treated surfaces. Since the bubbles are less than 1 micron in size, they are able to reach even the smallest holes and corners. For this reason, ultrasonic cleaning is the most effective method for degreasing metal parts and components with complex geometries, regardless of the type of material: cast iron, steel, aluminum, copper, bronze, titanium, engineering plastics, or even rubber.
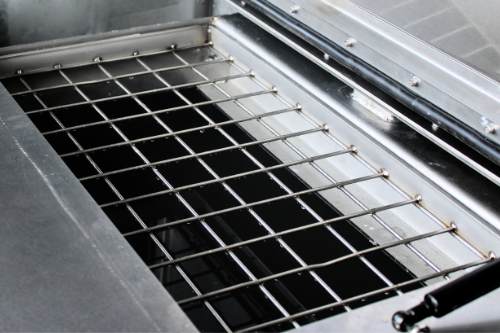
Ultrasonic tank for degreasing parts.
Advantages of Ultrasonic Degreasing
1. Deep Cleaning Even in Inaccessible Areas
Ultrasonic cavitation acts evenly across the entire surface of the part, including cavities, grooves, holes, threads, internal geometries, and rough surfaces. This ensures complete and even cleaning.
2. Respect for Parts: No Wear or Deformation
Without mechanical contact, parts are not scratched, deformed, or damaged, making it perfect for delicate or high-precision components, such as optical, electronic, medical, or watchmaking parts.
3. Energy Efficiency and Sustainability
Modern ultrasonic equipment like that of DCM Ultrasonic is designed to consume less energy than other industrial cleaning methods. Furthermore, the use of biodegradable detergents and liquid recirculation systems reduce the use of chemicals and the environmental impact.
4. Reduction in Cleaning Times
Ultrasonic degreasing is a fast process. Parts are cleaned in just a few minutes, significantly increasing plant productivity.
5. Automation and Labor Savings
Ultrasonic systems can be fully automated, eliminating the need for constant operator intervention. This allows human resources to be dedicated to more critical tasks and reduces occupational hazards.
6. Adaptability to Different Sectors
From heavy industry to the manufacturing of microelectronic components, ultrasonic degreasing is a versatile technology that adapts to very diverse needs and part sizes.
Recommendations for Choosing an Ultrasonic Degreasing Machine
When choosing ultrasonic degreasing equipment, it is important to consider:- Tank size: depending on the dimensions of the parts to be cleaned.
- Generator power: higher power, greater cavitation capacity.
- Frequency: Lower frequencies (20-30 kHz) are ideal for coarse dirt; higher frequencies (40-80 kHz) for delicate parts.
- Construction material: Stainless steel is essential for a long lifespan.
- Filtration and recirculation system: Improves performance and extends the life of the cleaning fluid.
- Automation and connectivity: Ideal for advanced industrial processes and remote monitoring.
Ultrasonic degreasing has established itself as the best alternative to traditional industrial cleaning methods, thanks to its precision, effectiveness, speed, and respect for parts and the environment. For both maintenance tasks and manufacturing processes, this technology represents a smart and profitable investment for any industry.
Are you looking to improve the efficiency of your industrial cleaning processes? Do you want to remove tough contaminants without damaging your parts? Ultrasonic degreasing is the answer. Contact us and discover how our ultrasonic machines can transform your operations.