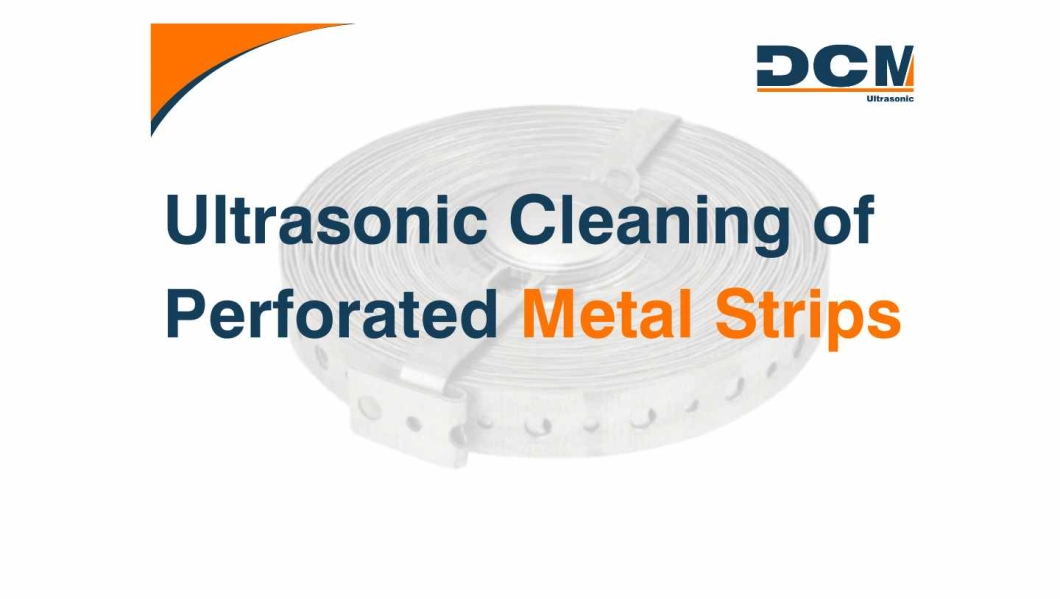
Ultrasonic cleaning of perforated metal strips
Perforated Metal Strips
Perforated metal strips are continuous metal bands that feature a series of holes or perforations evenly distributed along their surface. These perforations can vary in size, shape and pattern, depending on their specific application. They are widely used in sectors such as construction, for supports and fasteners; in the automotive industry, as structural components; and in the manufacturing of electronic products, serving as conductive or heat dissipation elements.Challenges in cleaning perforated metal strips
The manufacturing and handling process of these strips involves their exposure to various contaminants, such as:- Lubricant and oil residues: Used during stamping and forming of the metal.
- Metal particles: Resulting from cutting or perforation processes.
- Dust and environmental dirt: Which adhere during storage or transport.
The complexity of its geometry, with multiple perforations and possible hard-to-reach areas, makes manual cleaning or cleaning by conventional methods ineffective and laborious. In addition, the use of aggressive chemicals can damage the material or leave unwanted residues.
REQUEST INFORMATION ABOUT MACHINES FOR CLEANING METAL TRIMS
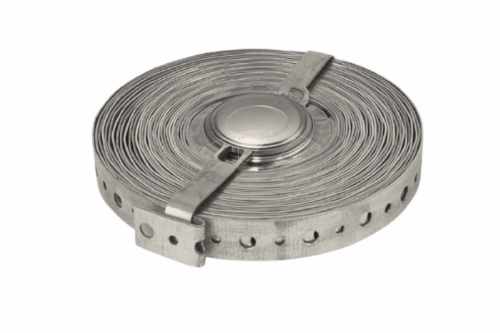
Metal components used in electronic applications, such as connectors, sockets and transistors, are manufactured in continuous profiles before being cut to their final size. During processes such as metal stamping and drawing, large amounts of dust and debris are generated that must be removed before later stages such as coating or final assembly of the part. Ultrasonic cleaning of continuous metal cords offers multiple benefits and is especially effective where traditional methods such as brushing or chemical cleaning may be too aggressive or cause mechanical damage. In addition, the removed contaminants are continuously filtered and removed from the in-line ultrasonic cleaning system, ensuring a consistent, high-level cleaning quality.
Ultrasonic Cleaning
Ultrasonic cleaning is based on the generation of high-frequency sound waves (generally between 20 and 40 kHz) that are transmitted through a liquid, forming microbubbles in the process known as cavitation. These bubbles implode upon contact with the surface of the submerged object, effectively releasing and eliminating contaminants without damaging the base material.
Advantages of Ultrasonic Cleaning on Perforated Metal Strips
1. Efficiency in the Removal of Contaminants:
Cavitation allows the removal of oil residues, metal particles and other impurities even in perforations and hard-to-reach areas.
2. Non-Destructive Process:
Unlike abrasive methods, ultrasound cleans without wearing down or altering the dimensions or properties of the material.
3. Reduction in the Use of Chemicals:
In many cases, water with mild detergents is sufficient, minimizing the environmental impact and costs associated with handling chemicals.
4. Saving Time and Labor:
Automating the process allows cleaning large volumes of material in less time and with minimal human intervention.
5. Consistency and Uniform Quality:
Homogeneous cleaning is achieved across the entire surface of the strip, ensuring the quality of the final product.
SEE ULTRASONIC CLEANING MACHINES
Implementation of Ultrasonic Cleaning in Metal Strip Production Lines
To effectively integrate ultrasonic cleaning into industrial processes, it is essential to consider:
Cleaning System Design:
Equipment adapted to the width and speed of the strips, allowing in-line cleaning without interrupting production.
Cleaning Liquid Selection:
Depending on the type of contaminant and strip material, aqueous solutions with specific detergents are chosen to optimize cleaning without damaging the metal.
Operating Parameter Control:
Adjustment of the frequency and power of the ultrasound, as well as the temperature of the liquid, to maximize the efficiency of the process.
Equipment Maintenance:
Regular cleaning of the tanks and periodic replacement of the liquid to ensure constant performance and extend the life of the system.
Leading companies in the manufacture of electronic components have adopted ultrasonic cleaning to ensure the purity of their perforated metal strips, essential in the production of circuits and connections. Likewise, in the automotive industry, this method has improved the quality of critical parts, reducing failures and increasing vehicle reliability.
Applications:
- Removing stubborn dirt
- Endless metal strips of various widths
- Individual line speeds
- Sensitive and thin materials
- Sharp-edged metal strips
- Complex stamped/perforated metal strips
DCM Ultrasonic, specialists in ultrasonic cleaning for all types of industrial parts and components!