Tue, 20 May 2025 12:38:24 +0200
Main advantages of using ultrasound for packaging or bottling lines
DISCOVER OUR FOAM CONTROL SYSTEM
The ultrasonic system offers an elegant solution: ultrasonic transducers are installed near the filling spouts or above the foam accumulation zone, without touching the liquid, and their activation eliminates the foam instantly. This allows the line to run continuously, reducing waste and maintaining consistent quality.
Foam Control System Highlights
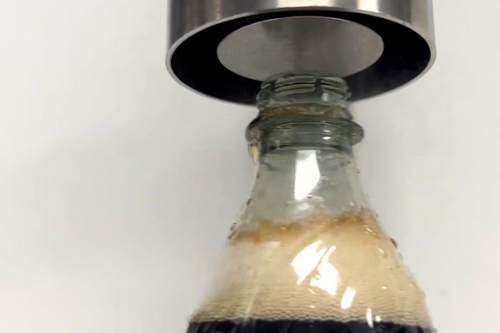
CAN WE HELP YOU CONTROL FOAM IN YOUR PRODUCTION LINES?
In an industrial environment where efficiency, automation, and sustainability are top priorities, having a reliable foam control system is no longer optional, but essential. Ultrasonic technology has proven to be a modern, chemical-free, precise, and easily integrable solution.
If your process plant is facing foam problems in its filling and packaging lines, DCM Ultrasonic foam control system is the ultimate tool to solve them effectively and without complications. We are ready to help you improve your production, reduce costs, and meet the highest quality standards.
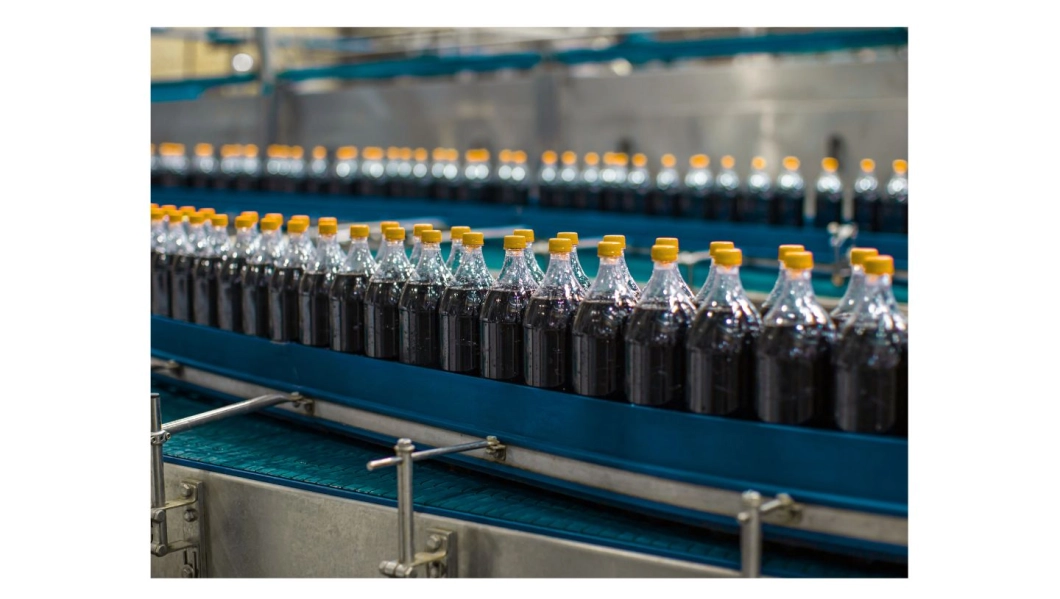
News
Ultrasonic System for Foam Control in Process Plants
20 May de 2025
Foam control is a constant challenge in many process plants, especially in sectors such as food, beverages, chemicals, and pharmaceuticals. Within these facilities, packaging and bottling lines are particularly sensitive to problems arising from foam generation: overflows, unscheduled shutdowns, product waste, and loss of operational efficiency. Fortunately, ultrasonic foam control technology has emerged as an effective, clean, and highly automated solution.The Foam Problem in Process Plants
During filling and packaging processes, bubbles and foam are commonly generated as a result of liquid agitation, the presence of surfactants, or dissolved gases. This foam can accumulate and overflow containers, creating several complications:- Production delays due to frequent shutdowns for cleaning.
- Product loss due to spills or residues in the system.
- Inconsistencies in fill volume, affecting quality and regulatory compliance.
- Added costs in cleaning, reprocessing, and maintenance.
Foam Control with Ultrasonic Technology
Ultrasonic foam control technology uses high-frequency acoustic waves (between 20 and 100 kHz) generated by piezoelectric transducers, which propagate through the air and act directly on the foam. These waves cause the bubbles to rupture, disintegrating the foam without physical contact and without adding chemicals to the process.Main advantages of using ultrasound for packaging or bottling lines
- No chemical additives: ideal for food or pharmaceutical products where product purity is essential.
- Does not contaminate the product or the equipment.
- Immediate action: Foam disappears in real time, avoiding downtime or losses.
- Full automation: Systems can be integrated into the line with PLC control.
- Compatible with CIP (Clean in Place) processes.
- High energy efficiency: Minimum consumption compared to other active systems.
DISCOVER OUR FOAM CONTROL SYSTEM
Specific application in packaging and bottling lines
Packaging and bottling lines represent one of the most demanding environments for foam control in processing plants. On these lines, the rapid filling of bottles, cans, or containers can generate foam in a matter of seconds. If this foam is not controlled in a timely manner, the equipment must be stopped, and the product can be wasted.
The ultrasonic system offers an elegant solution: ultrasonic transducers are installed near the filling spouts or above the foam accumulation zone, without touching the liquid, and their activation eliminates the foam instantly. This allows the line to run continuously, reducing waste and maintaining consistent quality.
Ultrasonic System for Foam Control
At DCM Ultrasonic, we have developed a solution specifically designed to eliminate foam in bottling and packaging lines: the Defoaming System. Our range of NexTgen Inside ultrasonic generators is optimized to drive piezoelectric transducers operating over a wide frequency range (from a few kHz to 100 kHz), reaching power levels of up to 3000 W peak.Foam Control System Highlights
- Robust industrial design, ideal for 24/7 operation.
- Full compatibility with automated environments thanks to its PLC, Ethernet, or RS485 interfaces.
- Intelligent visualization and control with multi-color LED buttons and touchscreen.
- Configure ultrasound cycles and duration.
- View parameters in real time: power, frequency, impedance, current.
- Perform diagnostics and log events.
- Monitor multiple generators from a central interface.
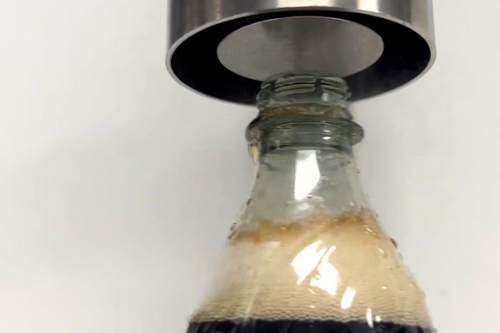
Benefits of Ultrasonic Foam Control Systems for Process Plants
- Reduction in unscheduled downtime.
- Elimination of the use of chemical antifoams.
- Increased filling speed without the risk of overfoaming.
- Lower energy consumption compared to traditional systems.
- Improved overall system efficiency (OEE).
- Greater hygiene and compliance with food and pharmaceutical regulations.
- Rapid payback thanks to savings in product, time, and maintenance.
Sectors where foam control is critical
Ultrasonic foam control technology is applicable to multiple industries, including:- Beverages and juices: packaging of carbonated or viscous liquids.
- Beer and fermentation: where foam formation is very aggressive.
- Detergents and cosmetics: filling of foaming products.
- Pharmaceuticals and nutraceuticals: liquid products sensitive to contamination.
- Chemical and petrochemical industries: fluid filling with surfactants.
CAN WE HELP YOU CONTROL FOAM IN YOUR PRODUCTION LINES?
In an industrial environment where efficiency, automation, and sustainability are top priorities, having a reliable foam control system is no longer optional, but essential. Ultrasonic technology has proven to be a modern, chemical-free, precise, and easily integrable solution.
If your process plant is facing foam problems in its filling and packaging lines, DCM Ultrasonic foam control system is the ultimate tool to solve them effectively and without complications. We are ready to help you improve your production, reduce costs, and meet the highest quality standards.